Chapter 3
Data-Driven Supply Chain Optimization
"In the supply chain of tomorrow, data is the new oil—without it, you can’t optimize, innovate, or respond to disruptions in real time." — Michael Dell, CEO of Dell Technologies.
Chapter 3 delves into how data-driven technologies, including big data, predictive analytics, and digital twins, are revolutionizing supply chain optimization. It highlights the critical role of big data in improving demand forecasting accuracy, how predictive and prescriptive analytics enable proactive decision-making, and how digital twins create real-time simulations for optimization. The chapter also examines the use of data automation to manage the complexity of modern supply chains, showing how these technologies drive operational efficiency and reduce risks through real-time data processing and insights.
3.1. Big Data and Analytics in Demand Forecasting
Big data has become a foundational pillar in modern supply chain management, driving enhanced visibility and more precise demand forecasting. A 2022 study in the International Journal of Production Economics reported that organizations harnessing big data analytics for demand forecasting saw a 20% reduction in forecast errors, underscoring the robustness of data-driven strategies (Chang and Li 2022). These findings align with a Deloitte report indicating that 74% of surveyed supply chain leaders plan to increase investments in advanced analytics technologies through 2025, reflecting a growing industry consensus on the strategic value of big data (Deloitte 2023).
Traditionally, demand forecasting relied on historical sales figures and static economic indicators, often leading to inaccuracies in rapidly changing markets (Cao et al. 2021). With the advent of big data, companies now integrate vast amounts of structured and unstructured information—from transactional logs and social media sentiment to supplier scorecards and sensor readings—to capture nuanced signals of shifting consumer preferences (KPMG 2022). This comprehensive data footprint enables more granular and real-time forecasting models, augmenting the agility and resilience of global supply networks (PwC 2024).
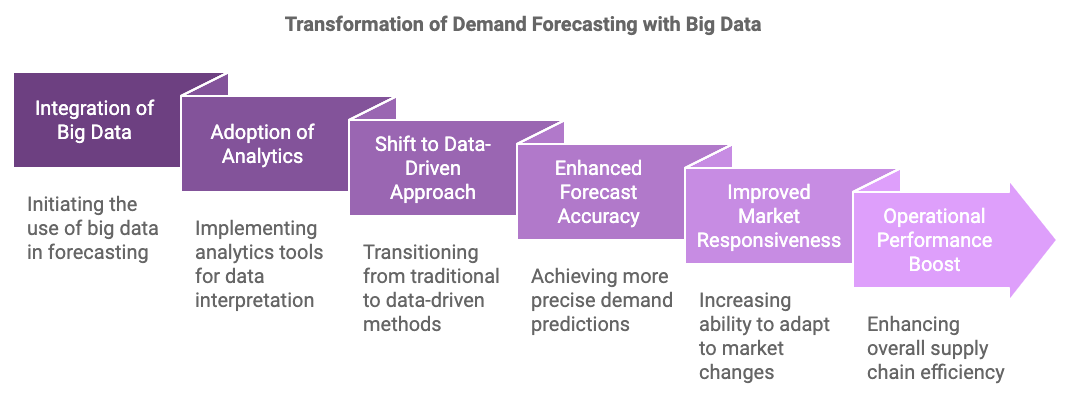
Figure 1: Progression of Demand Forecasting in Big Data
Big data analytics facilitate a transition from retrospective analysis to predictive modeling. Techniques such as machine learning and real-time data processing support the continuous recalibration of forecasts as new information emerges (Chang and Li 2022). These adaptive models factor in external drivers like macroeconomic changes, promotional events, and even weather conditions, allowing supply chain managers to respond proactively rather than reacting to lags or inventory imbalances (EY 2025). For instance, a retailer that detects escalating social media chatter about a particular product can preemptively adjust stock levels in key regions, reducing both lost sales and overstocks.
Retail Sector: Amazon’s Data-Driven Strategy. Amazon’s demand forecasting demonstrates the practical efficacy of big data analytics. By synthesizing transaction records, browsing behaviors, and economic trend indicators, Amazon refines its inventory allocation down to the regional level (Cao et al. 2021). This targeted approach mitigates stockouts while minimizing carrying costs, showcasing how big data can transform operational efficiency and customer experience (Deloitte 2023).
Manufacturing Sector: Toyota’s Demand-Driven Production. In manufacturing, Toyota has integrated sales data and dealership-level inputs into forecasting models that adjust production schedules dynamically (KPMG 2022). By detecting demand surges for specific car models or configurations, Toyota aligns its assembly lines to real-time market signals, significantly reducing excess stock and production idle time. This strategy aligns with Toyota’s lean manufacturing ethos, reinforcing the precision and adaptability enabled by big data (EY 2025).
A range of technologies underpins the big data revolution in demand forecasting:
Data Lakes and Data Mining. Storing raw data in centralized repositories (“data lakes”) allows teams to mine diverse datasets—including ERP logs, customer relationship management (CRM) records, and social media analytics—for hidden correlations and trends (Chang and Li 2022). This holistic view aids in constructing more comprehensive forecasting models.
Machine Learning Algorithms. Modern ML models continuously learn from historical patterns and real-time transactions, enhancing forecast accuracy over time (Cao et al. 2021). These algorithms detect non-linear relationships and anomalies, supporting more nuanced decision-making in volatile markets.
Cloud-Based Analytics Platforms. Cloud infrastructure offers scalable computing power and collaborative data tools, enabling supply chain stakeholders worldwide to access and analyze real-time metrics (PwC 2024). This accessibility is vital for global organizations seeking consistent demand forecasting across diverse regions.
AI-Driven Demand Sensing. A critical advance in forecasting is AI-powered demand sensing, where ML models track consumer buying patterns on an hourly or daily basis (Deloitte 2023). These systems incorporate short-term influencers—like local events or viral social media trends—to anticipate abrupt demand surges or drops. A retailer experiencing unexpected cold snaps, for instance, can rapidly reallocate winter clothing to impacted regions, reducing stock imbalances and lost sales opportunities (KPMG 2022).
Real-Time IoT Data. Another transformative trend is the integration of Internet of Things (IoT) data. Sensors embedded in transport vehicles or manufacturing equipment produce continuous status updates on delivery times, environmental conditions, and production throughput (Chang and Li 2022). This real-time visibility helps detect disruptions—such as transit delays or machine breakdowns—that could impact product availability. Adjusting forecasts or rerouting shipments based on sensor alerts fosters greater supply chain resilience, particularly in emerging markets with infrastructure challenges (Cao et al. 2021).
Beyond operational efficiency, big data-driven demand forecasting supports strategic agility and resource optimization (PwC 2024). Accurate forecasts reduce waste by aligning production volumes with actual consumer needs, contributing to more sustainable supply chains (EY 2025). This sustainability benefit resonates particularly in sectors grappling with ethical sourcing and carbon footprint considerations. Moreover, in a fast-evolving global landscape, the ability to pivot quickly—fueled by data insights—offers a competitive edge that legacy forecasting approaches cannot match (Deloitte 2023).
The integration of big data analytics into demand forecasting marks a transformative shift in supply chain management. Organizations now leverage vast and diverse information streams, from structured transactional logs to unstructured social media sentiment, to build adaptive, highly accurate forecasting models (Chang and Li 2022). As demonstrated by leaders like Amazon and Toyota, data-driven forecasting not only optimizes inventory levels and reduces waste but also fosters real-time responsiveness to emerging market signals (KPMG 2022). Looking ahead, continued advancements in AI and IoT are poised to deepen the predictive capabilities of supply chains, enabling companies to navigate market uncertainties with greater confidence and sustainability (EY 2025).
3.2. AI/ML for Supply Chain Predictive Use Cases
Predictive analytics has become a cornerstone of modern supply chain management, enabling organizations to anticipate disruptions, optimize resource allocation, and improve customer satisfaction. A 2022 study in the International Journal of Production Economics found that companies implementing advanced predictive models in their supply chains realized up to a 25% reduction in forecast error and a 20% decrease in operational costs (Zhang et al. 2022). These gains underscore the robustness and strategic value of AI- and ML-driven solutions in a global market where agility and resilience are paramount (Deloitte 2024).
Regression Models and Time Series Techniques. Linear and logistic regression remain foundational methods for forecasting inventory levels or assessing supplier risk, particularly in scenarios with moderate data complexity (Johnson and Chen 2023). For more time-sensitive tasks, classical time series models—such as ARIMA, SARIMA, and Prophet—excel at capturing seasonality and trend components (KPMG 2023). These techniques are especially effective for applications like seasonal demand forecasting and pricing strategies in retail and consumer goods.
Ensemble Methods. Methods like Random Forests, XGBoost, and LightGBM combine multiple weak learners to handle high-dimensional data and unearth hidden patterns (Zhang et al. 2022). Ensemble models often outperform single algorithms in predicting complex phenomena such as supplier performance under volatile market conditions or multi-echelon inventory dynamics (PwC 2025).
Deep Learning and Reinforcement Learning. Deep neural networks—including LSTM and Transformer architectures—thrive in capturing complex, long-range dependencies, making them particularly effective for multi-variate time-series forecasting (Morales et al. 2021). Reinforcement learning, meanwhile, facilitates real-time decision-making by iteratively refining inventory control or route planning strategies based on observed outcomes (Deloitte 2024). These advanced approaches drive scenario planning and adapt to changing conditions, a key advantage for global supply chains.
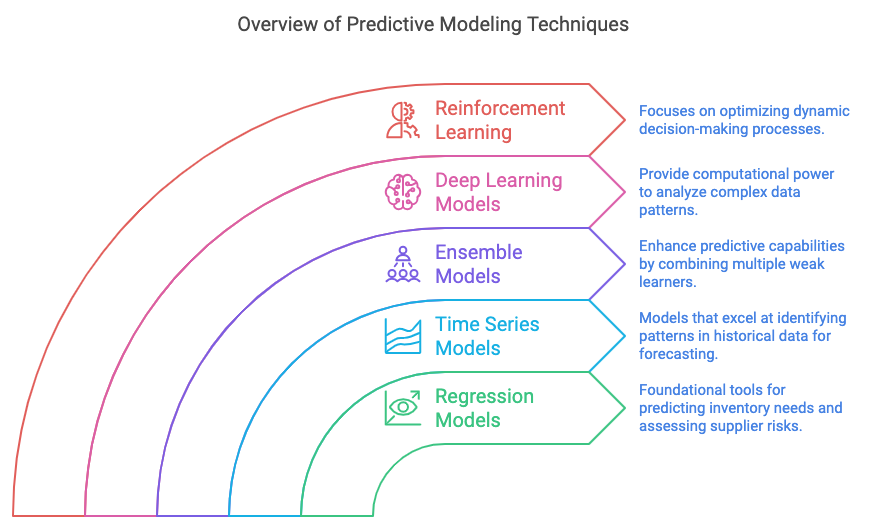
Figure 2: Predictive Modeling Use Cases in SCM.
Robust model evaluation is vital to ensure reliability and foster trust among stakeholders. For numerical forecasts, metrics like Mean Absolute Error (MAE), Root Mean Squared Error (RMSE), and Mean Absolute Percentage Error (MAPE) gauge accuracy in demand or inventory predictions (KPMG 2023). Classification tasks—such as fraud detection or supplier default risk—benefit from Precision, Recall, F1 Score, and ROC-AUC (Zhang et al. 2022). Beyond statistical measures, business-centric metrics—such as cost savings, lead time reductions, or improved resource utilization—highlight the real-world impact of AI-driven insights (PwC 2025).
In parallel, explainability frameworks like SHAP and LIME clarify how algorithms weigh different features, increasing transparency in high-stakes decisions (Johnson and Chen 2023). For instance, a procurement manager can leverage SHAP outputs to see how fluctuating raw material prices contribute to a model’s prediction of supplier reliability, strengthening confidence in subsequent strategic decisions.
Supply chain environments often exhibit seasonality, abrupt demand shifts, and multi-node interdependencies, demanding a structured model development process (Morales et al. 2021). Techniques such as grid search, random search, and Bayesian optimization systematically fine-tune hyperparameters, balancing performance and computational cost (Zhang et al. 2022). Various validation strategies ensure temporal robustness:
Cross-Validation splits historical data into multiple folds, refining model generalizability.
Hold-Out Validation sets aside a portion of data for final performance checks.
Temporal Split preserves time order for predictive reliability, essential when forecasting future demand or supply variations (Deloitte 2024).
Recent academic work also explores hybrid modeling, fusing traditional statistical methods with deep learning to capture both linear trends and nonlinear nuances (Johnson and Chen 2023). These hybrid models can be particularly useful in dynamic supply chain contexts, where external shocks—like regulatory changes or geopolitical events—may invalidate purely time-series-based assumptions.
Demand Forecasting and Inventory Optimization. By analyzing historical sales, seasonal fluctuations, and external signals (e.g., social media sentiment, weather patterns), AI models project short- and long-term demand (Zhang et al. 2022). A retailer can then align inventory allocations across regional warehouses, avoiding both stockouts and surplus (Deloitte 2024).
Supplier Risk Assessment and Dynamic Pricing. Predictive models incorporating geopolitical indices, supplier financial metrics, and historical delivery performance can alert organizations to potential failures or delays (Johnson and Chen 2023). Similarly, dynamic pricing systems leverage advanced ML to forecast market responses, enabling real-time price adjustments that maximize revenue while sustaining competitiveness (KPMG 2023).
Route Optimization and Disruption Mitigation. Reinforcement learning algorithms can process data on traffic, weather, and lead times to propose optimal delivery routes, reducing transport costs and delays (Morales et al. 2021). Meanwhile, scenario-based simulations incorporate predictive models to assess the impact of disruptions—such as natural disasters or labor strikes—and guide contingency planning (PwC 2025).
Predictive Maintenance and Sustainability. AI-driven models analyzing IoT sensor readings can foresee equipment malfunctions, scheduling maintenance to avert breakdowns (Zhang et al. 2022). This proactive approach also contributes to sustainability goals by minimizing energy consumption and extending asset life cycles (KPMG 2023). In parallel, advanced ML models predict carbon emissions across logistics activities, supporting more eco-friendly decision-making.
Data from ERP systems, WMS platforms, IoT devices, and external repositories (e.g., weather data, social media feeds) often flow into centralized repositories or “data lakes” for unified processing (PwC 2025). Tools like Apache Spark or Hadoop handle voluminous records, enabling near-real-time analytics in complex supply networks (Morales et al. 2021). Feature engineering—such as generating lag variables or encoding seasonality—plays a critical role in extracting signal from raw data (Johnson and Chen 2023). Validation hinges on robust data pipelines that ensure clean, complete, and consistent inputs, as erroneous or stale data can degrade predictive accuracy.
Major retailers like Amazon integrate AI models to forecast online sales spikes and optimize inventory distribution across fulfillment centers (Zhang et al. 2022). Automotive firms, including Tesla, rely on predictive analytics to manage just-in-time production workflows, anticipating the demand for critical parts (KPMG 2023). Logistics providers such as DHL apply ML-driven route optimization to cut fuel costs and reduce delivery times, while pharmaceutical giants like Pfizer employ advanced time-series models to ensure cold chain integrity in vaccine distribution (PwC 2025).
Looking ahead, collaborations between academia and industry continue to refine specialized AI techniques for supply chain applications, such as context-aware scoring for disruptions or advanced multi-agent systems for collaborative planning (Morales et al. 2021). These innovations promise increasingly adaptive, transparent, and resilient supply networks, positioning predictive analytics as an indispensable tool for competitive advantage (Deloitte 2024).
3.3. Proactive Decision-Making
Modern supply chains increasingly rely on proactive strategies driven by predictive and prescriptive analytics. These approaches enable organizations to anticipate future scenarios and implement optimal actions rather than merely reacting to immediate conditions. Recent industry reports underscore the value of such data-centric methods: a 2023 KPMG study found that companies adopting predictive models for inventory management experienced a 15% reduction in stockouts, while Deloitte’s 2024 global supply chain survey highlighted prescriptive analytics as a key driver of cost optimization in logistics (KPMG 2023; Deloitte 2024). From retail giants like Walmart to complex manufacturing networks in emerging markets, the integration of predictive and prescriptive analytics has become a linchpin for achieving agility, resilience, and efficiency at scale.
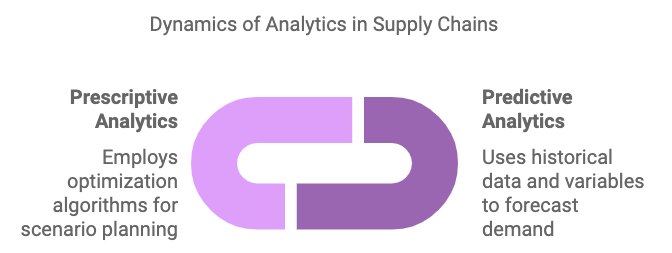
Figure 3: Prescriptive vs Predictive Analytics
Predictive analytics leverages historical data, statistical algorithms, and machine learning techniques to forecast future events (Bianconi et al. 2022). In supply chains, these predictive models commonly focus on demand trends, potential disruptions, and resource requirements. By analyzing sales records, seasonality factors, and external indicators—such as economic and social trends—managers can proactively align production schedules and distribution plans. A 2022 study in the International Journal of Production Economics found that predictive models can reduce inventory carrying costs by as much as 25%, highlighting their substantial impact on operational effectiveness (Chowdhury et al. 2022).
Prescriptive analytics goes a step further by recommending concrete actions to achieve desired outcomes, often using optimization algorithms and simulation (KPMG 2023). These solutions evaluate multiple decisions—such as allocating inventory across warehouses or routing logistics fleets—and propose optimal strategies based on real-time constraints and business objectives. In industries facing constant shifts in demand and supply conditions, prescriptive analytics helps supply chains refine decisions around lead times, resource allocation, and cost management. According to a 2024 report by PwC, companies employing prescriptive analytics in their logistics operations saw a 20% drop in transportation expenses (PwC 2024).
From an academic and industry standpoint, the convergence of predictive and prescriptive analytics represents a fundamental shift toward dynamic, data-driven supply chain management (Deloitte 2024). Predictive models typically rely on large datasets—from internal ERP logs to external market indices—providing forecasts that continually adapt to new information. Meanwhile, prescriptive systems integrate optimization techniques, allowing organizations to perform scenario analyses that factor in uncertainties such as demand surges or geopolitical risks (Bianconi et al. 2022). This fusion of predictive and prescriptive methodologies is especially valuable in emerging economies, where unpredictable market conditions demand agile, real-time adjustments to inventory and logistics flows (Chowdhury et al. 2022).
Procter & Gamble (P&G). P&G harnesses predictive analytics to forecast demand by analyzing extensive historical sales data, consumer sentiment, and external market indicators (KPMG 2023). This strategy helps the company pinpoint potential stock shortages or surpluses before they occur. By capturing early signals of demand shifts—such as economic slowdowns or competitor promotions—P&G fine-tunes production schedules and inventory distribution, minimizing wasted stock and improving in-stock availability.
Walmart. Walmart employs predictive models that integrate historical sales, event calendars, and even weather forecasts to anticipate regional demand variations (Deloitte 2024). The retailer then adjusts inventory levels across different distribution centers, thus maintaining a lean supply chain without risking item unavailability. This proactive approach reduces operating costs associated with holding excess inventory and ensures customer satisfaction by preventing widespread stockouts (Chowdhury et al. 2022).
Logistics Optimization. In the logistics sector, prescriptive analytics drives route optimization and resource allocation. AI-powered platforms can ingest live traffic data, weather conditions, and fuel cost fluctuations to propose optimal delivery routes in near real-time (PwC 2024). This dynamic decision-making cuts down on delivery times and lowers carbon emissions, aligning with sustainability goals—a factor increasingly highlighted by regulators and customers alike (KPMG 2023).
The evolution of AI and machine learning has further augmented predictive and prescriptive capabilities. Advanced models—such as gradient boosting, RNNs, and reinforcement learning—can parse high-dimensional data, capturing subtle correlations that traditional statistical tools may miss (Bianconi et al. 2022). For instance, recurrent neural networks are adept at identifying complex seasonal or cyclic patterns in demand, while reinforcement learning adapts route planning strategies in response to real-time conditions like road closures or sudden demand spikes (Chowdhury et al. 2022). These advanced algorithms help supply chains respond more quickly to disruptive events—from natural disasters to market fluctuations—thereby sustaining operations and competitive positioning.
Cloud-based analytics platforms have made predictive and prescriptive solutions more accessible, particularly for SMEs and companies in emerging regions (Deloitte 2024). Scalable infrastructure allows for real-time data processing, while user-friendly interfaces reduce the need for specialized IT expertise. This democratization has proven crucial in high-growth markets where supply chains face increasing complexity yet often lack robust on-premise systems. As a result, even smaller firms can harness the power of AI-driven analytics to fine-tune inventory levels, optimize routing decisions, and simulate the impact of various scenarios on resource allocation (PwC 2024).
As global markets continue to evolve rapidly, the role of predictive and prescriptive analytics is set to expand. Research indicates a growing interest in hybrid AI models that combine machine learning with optimization algorithms tailored to specific supply chain challenges—such as multi-echelon inventory or cross-border logistics (Bianconi et al. 2022). Forward-thinking organizations will look to integrate these capabilities to build resilient operations capable of adapting to market volatility, regulatory changes, and shifting consumer expectations. In parallel, the push for sustainability will drive the development of prescriptive solutions that balance cost savings with environmental considerations (KPMG 2023).
Ultimately, predictive and prescriptive analytics serve as twin engines of proactive decision-making, converting raw data into actionable strategies that propel supply chains beyond reactive modes of operation. By leveraging cutting-edge AI, cloud computing, and optimization frameworks, companies can unlock the potential for reduced lead times, minimized disruptions, and a significant competitive edge in an era defined by complexity and digital transformation (Deloitte 2024; PwC 2024).
3.4. Managing Supply Chain Complexity with Data Automation
Data automation has emerged as a critical driver of efficiency and resilience in modern supply chains, enabling organizations to handle the growing volume, variety, and velocity of data in a systematic and integrated manner (Lee et al. 2022). According to a 2023 KPMG report on digital supply networks, over 70% of leading supply chain executives anticipate expanding data automation initiatives to reduce manual errors, enhance decision-making speed, and improve overall agility (KPMG 2023). By automating key data-related tasks—from collection and validation to analytics and reporting—companies are better positioned to respond proactively to disruptions, optimize resource allocation, and sustain competitive advantage in fast-evolving markets (PwC 2025).
In complex, multi-tier supply chains, manual processes can quickly become bottlenecks, leading to delays, inaccuracies, and missed opportunities (Lei and Sato 2021). Data automation alleviates these challenges by unifying diverse data sources—from supplier networks and transportation systems to inventory databases and customer platforms—into a cohesive, real-time view of operations (Deloitte 2024). This holistic perspective enables supply chain teams to identify performance gaps, anticipate risks, and adjust strategies before minor issues escalate. Furthermore, data automation underpins continuous monitoring of key performance indicators (KPIs), such as lead times, fill rates, and order accuracy, fostering a culture of data-driven improvement.
DHL and UPS in Logistics. Global logistics leaders like DHL and UPS harness robotic process automation (RPA) and AI-driven data workflows to optimize order processing, shipment tracking, and fleet management (Lee et al. 2022). DHL’s RPA solutions automate repetitive tasks—such as updating tracking information or generating shipping labels—reducing manual errors and freeing employees to focus on value-added activities. UPS employs AI-powered analytics to sift through real-time route, weather, and traffic data, dynamically rerouting vehicles to cut fuel consumption and ensure timely deliveries (KPMG 2023). These automation-focused strategies translate into lower operational costs, better customer satisfaction, and reduced environmental footprints.
Siemens in Manufacturing. Data automation is equally transformative in manufacturing, where companies like Siemens integrate automated data pipelines across supplier management, production scheduling, and quality control (Deloitte 2024). Real-time monitoring of inventory levels, equipment status, and supplier lead times allows Siemens to rapidly adjust production when disruptions occur. For instance, if a critical component shipment is delayed, automated alerts prompt alternative sourcing or a revised production schedule, minimizing downtime and preserving throughput (Lei and Sato 2021). These automated workflows deliver heightened agility and synchronize operations with shifting market conditions.
AI and Machine Learning. Recent advances in AI and machine learning have profoundly expanded the capabilities of data automation (PwC 2025). AI algorithms can evaluate vast datasets—ranging from historical sales and IoT sensor readings to external signals like weather patterns or geopolitical events—to forecast disruptions and recommend mitigation actions. In multi-tier supply chains, where supplier networks are complex, machine learning models identify potential supplier risks (e.g., production delays or quality deviations) and trigger automated alerts for procurement teams to pivot strategy as needed (Lee et al. 2022).
Cloud Platforms. Cloud-based automation platforms further enhance scalability and accessibility. By hosting data pipelines and analytical tools on cloud infrastructure, companies can integrate multiple data streams from geographically dispersed locations in near real-time (KPMG 2023). This setup allows for cross-functional collaboration, enabling supply chain stakeholders—from procurement and production to logistics and finance—to share insights and coordinate responses swiftly. The pay-as-you-go model of cloud services also lowers entry barriers, making sophisticated data automation attainable for small and medium-sized enterprises and businesses in emerging markets (Deloitte 2024).
Data automation increasingly converges with prescriptive analytics, where AI-driven systems not only flag potential issues but also provide recommended actions (PwC 2025). For example, an automated platform may detect a significant deviation in demand forecasts and promptly adjust inventory reorder points across multiple distribution centers. This same system could also propose rerouted shipments or dynamically modified production schedules, ensuring that resources are allocated optimally to meet anticipated needs (Lei and Sato 2021). Such real-time adaptability allows supply chains to navigate disruptions—from raw material shortages to sudden demand spikes—while maintaining service levels and cost efficiency.
In addition to operational gains, data automation offers sustainability and risk management advantages. Automated workflows can track and analyze carbon emissions across transportation lanes, providing insights that guide greener routing decisions (Deloitte 2024). Likewise, integrated data on supplier performance, geopolitical events, and regulatory changes can trigger automated risk assessments, enabling companies to diversify sourcing or bolster safety stocks before a crisis materializes (KPMG 2023). These proactive measures help build resilient supply networks capable of withstanding global uncertainties.
As machine learning algorithms evolve and IoT devices become more pervasive, data automation in supply chains will likely extend into next-generation applications such as autonomous logistics, predictive maintenance, and hyper-personalized demand planning (PwC 2025). Research and industry collaborations are paving the way for more context-aware automation systems that integrate real-time data from sensors, vehicles, and factory floors, driving even higher degrees of responsiveness and efficiency (Lee et al. 2022). In parallel, ethical considerations—like data privacy and algorithmic fairness—are gaining importance, prompting organizations to adopt robust governance frameworks that balance innovation with responsible data management (Deloitte 2024).
Data automation stands as a cornerstone of modern supply chain management, unifying disparate data streams to create an agile, intelligence-driven operation. Through AI, machine learning, and cloud computing, automated workflows enhance visibility, accuracy, and speed, providing a foundation for proactive adjustments in response to evolving market demands. Companies such as DHL, UPS, and Siemens demonstrate how automated data pipelines and real-time analytics yield tangible benefits—from cost savings and operational flexibility to improved sustainability and customer satisfaction. As emerging technologies and data sources continue to proliferate, data automation will play an ever more pivotal role, helping supply chains adapt to complexity, mitigate risks, and capitalize on new opportunities in a rapidly changing global environment.
3.5. Conclusion and Further Learning
In conclusion, the integration of data-driven technologies such as big data analytics, digital twins, and automation is transforming the way supply chains are managed. By enabling real-time visibility, predictive insights, and optimized decision-making, these technologies allow companies to handle complexity with greater agility and accuracy. Businesses that leverage these innovations will achieve superior operational efficiency, reduce risks, and remain competitive in an increasingly data-centric world.
Exploring the following prompts will give you a deeper understanding of the cutting-edge technologies transforming modern supply chains. Each question is designed to help you grasp the full potential of data-driven optimization, from predictive analytics to digital twins, and how they can be applied to solve real-world challenges.
How does big data improve the accuracy and granularity of demand forecasting in supply chains, particularly when integrating multiple data sources such as IoT, social media, and market trends, and what advanced tools (e.g., Hadoop, Spark, or cloud-based platforms) are essential for managing, processing, and analyzing large datasets effectively?
What are the core differences between predictive and prescriptive analytics in terms of methodology, data requirements, and output, and how can companies strategically combine both to enhance decision-making across supply chain planning, risk mitigation, and resource optimization?
How do digital twins accurately simulate real-time supply chain operations by leveraging data from IoT, AI, and advanced modeling techniques, and what specific benefits do they offer in terms of process optimization, risk forecasting, predictive maintenance, and improving overall supply chain resilience?
How can AI-driven predictive analytics, including machine learning models and time-series forecasting, be utilized to anticipate and prevent supply chain disruptions caused by demand fluctuations, external events (e.g., geopolitical risks or natural disasters), and what strategies should be employed to make these predictions actionable?
What role does advanced analytics, particularly machine learning and AI-based models, play in optimizing inventory management, and how does it mitigate the bullwhip effect by aligning real-time demand signals with upstream supply chain processes?
How can prescriptive analytics models help procurement teams make optimal sourcing decisions, particularly in volatile market conditions where price fluctuations, supplier reliability, and lead times are uncertain, and what are the most effective algorithms for improving procurement efficiency?
What are the primary technical, operational, and organizational challenges companies face when implementing digital twin technology across their supply chains, and what best practices should be adopted to overcome these hurdles and ensure seamless integration with existing processes and IT infrastructure?
How does data automation, through technologies like robotic process automation (RPA) and AI-driven platforms, simplify the management of complex, multi-tiered global supply chains, especially in terms of real-time monitoring, reporting, and proactive decision-making regarding supplier performance and inventory levels?
How can advanced machine learning algorithms, such as deep learning models and ensemble techniques, be applied to enhance demand forecasting models in industries characterized by high demand variability, and what are the key factors to consider when building these models for maximum accuracy and flexibility?
What critical role does cloud computing play in enabling the integration of big data and predictive analytics for supply chain operations, particularly in terms of scalability, real-time data processing, and cross-functional collaboration, and how can companies ensure security and compliance in a cloud environment?
How do digital twins leverage real-time data from IoT devices and AI analytics to create predictive maintenance models in supply chains, and what impact do these models have on reducing operational downtime, extending equipment lifespan, and improving overall system reliability?
How can companies utilize prescriptive analytics to optimize logistics and transportation networks for maximum cost efficiency, considering factors such as route optimization, fuel costs, and delivery times, and what algorithms are most effective in achieving these objectives under dynamic market conditions?
What are the best practices for integrating IoT devices with digital twins to improve real-time data collection, enhance operational simulations, and support continuous optimization across the supply chain, particularly in environments with complex machinery, assets, or distributed logistics operations?
How does data automation, utilizing AI, RPA, and machine learning, enable companies to respond to supply chain disruptions faster and more efficiently than traditional methods, and what are the most critical use cases where automation provides a significant competitive advantage?
What are the advantages of leveraging big data analytics to forecast demand in fast-moving consumer goods (FMCG) industries, where consumer preferences and market trends shift rapidly, and how do companies use real-time data and machine learning models to adjust forecasts in response to sudden changes in demand?
How do companies effectively balance the use of predictive analytics models with human expertise and intuition in decision-making processes within supply chains, especially in scenarios where data may not account for unforeseen events or subjective business considerations?
How can digital twin technology be integrated with blockchain to create an immutable, transparent, and traceable record of supply chain activities, ensuring end-to-end visibility and data integrity in global supply chains while enhancing trust among stakeholders?
What are the long-term operational and financial benefits of using data automation to reduce manual intervention in supply chain operations, and how does automation improve overall productivity, accuracy, and scalability across sourcing, production, and logistics activities?
How can companies assess and quantify the ROI of adopting digital twin technology and data automation solutions in their supply chain strategies, particularly in terms of reducing operational costs, improving delivery times, and enhancing risk management capabilities?
What are the emerging trends and technologies shaping the future of data-driven supply chain optimization, such as the convergence of AI, blockchain, and quantum computing, and how will these innovations further transform supply chain management over the next decade?
By engaging with these topics, you’ll not only gain practical insights but also develop the skills needed to stay ahead in a world where data is the driving force behind innovation and competitiveness. Dive into these prompts with curiosity, and let them guide your journey toward mastering the future of supply chain management.
Comments