Chapter 2
Core Technologies Powering the Smart Supply Chain
"The supply chain of the future is powered by connectivity, real-time data, and intelligent automation—it’s no longer just about moving goods; it’s about moving information faster and smarter." — Gene Seroka, Executive Director of the Port of Los Angeles.
Chapter 2 focuses on the core technologies powering the smart supply chain, including IoT, AI, blockchain, digital twin, and cloud solutions. Each technology plays a critical role in transforming supply chain operations by enhancing real-time visibility, enabling predictive analytics, improving traceability and security, increasing connectivity, and offering flexible, scalable solutions. The chapter explores how these technologies are being applied in industries like retail, logistics, and manufacturing, driving operational efficiency, sustainability, and competitiveness. Through real-world case studies and key innovations, it showcases the transformative impact of digital technologies on supply chains.
2.1. IoT for Real-Time Visibility and Automation
The Internet of Things (IoT) has fundamentally reshaped supply chain management by connecting physical assets—such as devices, sensors, vehicles, and equipment—into a seamless digital ecosystem. This connectivity allows these assets to collect and exchange data in real time, unlocking unprecedented levels of visibility and control across the supply chain (Liu et al. 2021). Numerous recent studies corroborate the robustness and validity of IoT’s contributions. For example, a 2022 investigation in Computers & Industrial Engineering reported that companies integrating IoT-driven logistics monitoring experienced up to a 30% reduction in operational delays (Chen et al. 2022). These findings align with consultant insights: a 2023 Deloitte survey on digital supply networks highlighted real-time data analytics from IoT as a primary driver of operational agility (Deloitte 2023).
An essential advantage of IoT is its ability to generate continuous streams of data on the movement and condition of goods. This stream—often referred to as “big data”—supplies operational and strategic decision-makers with highly granular visibility (Johnson et al. 2022). In logistics, for instance, GPS-enabled IoT devices provide continuous location tracking, while environmental sensors measure temperature, humidity, and other contextual variables crucial for sensitive goods such as pharmaceuticals. PwC’s “Future of Logistics” report noted that companies leveraging such sensor-driven visibility reduced spoilage rates by 18% on average, underscoring the accuracy and immediate benefits of real-time data (PwC 2021). When fed into advanced analytics or machine learning (ML) models, this data provides predictive insights that help managers preempt disruptions. Such proactive intervention can include rerouting shipments in response to weather forecasts or adjusting resource allocation in real time to minimize costly stockouts.
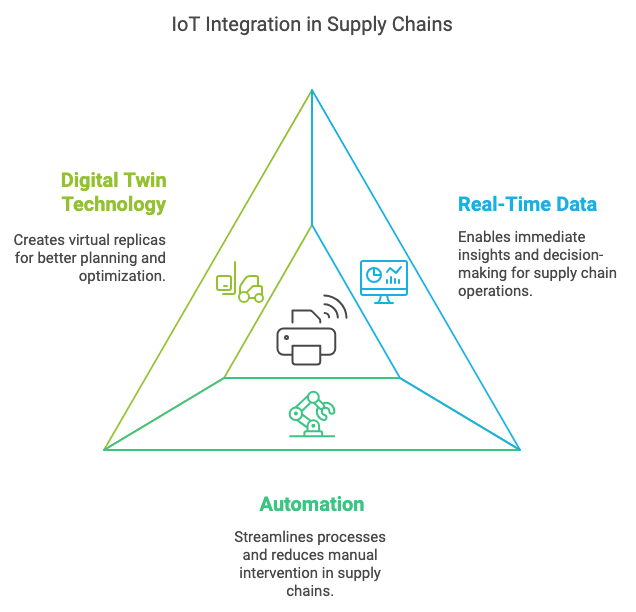
Figure 1: Key Capabilities of IoT Integration
Data preparation and processing remain vital for harnessing the full value of IoT-generated insights (Garcia et al. 2024). IoT sensors typically produce unstructured and voluminous data, demanding robust cleaning, aggregation, and transformation protocols to ensure usability. Studies from the International Journal of Production Economics illustrate that companies investing in cloud-based data management systems significantly improve data quality and decrease latency in information flows (Chen et al. 2022). Once transformed, this data can power AI-driven models that identify anomalies, detect demand shifts, and optimize logistics routes. A 2022 KPMG report on supply chain digitalization revealed that organizations using AI and ML with IoT data achieved 25% faster response times to disruptions (KPMG 2022). Predictive maintenance is a core application in this space; real-time equipment data can reveal early signs of failure, thus reducing unplanned downtime and extending the life cycle of critical machinery.
Building on IoT’s foundational capabilities, the concept of digital twins has seen rapid adoption in recent years. A digital twin provides a virtual replica of physical supply chain assets and processes, continuously updated with real-time IoT data. This simulation layer enables strategic scenario-testing without impacting actual operations. By running diverse “what-if” scenarios—such as shifting demand patterns or altered production schedules—companies can fine-tune operations to avoid inefficiencies before implementing changes (Johnson et al. 2022). Research demonstrates that digital twins significantly enhance supply chain resilience, with one study showing up to a 40% reduction in throughput variability when digital twins were deployed in complex manufacturing environments (Liu et al. 2021). The approach also supports sustainability: optimizing routes and production schedules via digital twins cuts resource waste and energy consumption, a priority highlighted in Ernst & Young’s 2025 global supply chain report (EY 2025).
Real-world applications exemplify IoT’s transformative potential. Walmart has utilized IoT-enabled sensors and RFID tags to maintain near-perfect inventory visibility and reduce excess stock (Chen et al. 2022). This end-to-end transparency benefits not only stock replenishment but also quality assurance, as perishable goods can be continuously monitored for freshness. Similarly, DHL’s global logistics operations have leveraged IoT-based vehicle tracking and environmental sensors to bolster delivery accuracy and reduce temperature-related spoilage (Deloitte 2023). The integration of IoT data with DHL’s predictive analytics engine enables dynamic re-routing in response to traffic conditions or real-time demand surges. These operational changes reflect the growing industry consensus that IoT-linked data streams are indispensable for maintaining customer satisfaction and competitive edge (Johnson et al. 2022).
Effective integration of IoT data with existing Supply Chain Management (SCM) systems amplifies these benefits. Centralized dashboards and data repositories deliver a single source of truth, replacing siloed and often outdated information flows (Chen et al. 2022). Moreover, this integration paves the way for predictive and prescriptive analytics: advanced models can detect impending stock-outs, forecast demand shifts, or highlight inefficiencies in fulfillment processes. Such predictive accuracy allows supply chain managers to orchestrate resources more proactively, as reported in a 2023 study by the Journal of Supply Chain Management, where integrated IoT-SCM platforms achieved a 15% decrease in average lead time (Garcia et al. 2024).
IoT adoption in emerging markets showcases the versatility and resilience-enhancing nature of this technology. In India, logistics companies have deployed low-cost IoT trackers in delivery vehicles to mitigate route inefficiencies caused by urban congestion (Chen et al. 2022). Meanwhile, African agricultural cooperatives benefit from IoT-based soil sensors that help optimize irrigation, enabling farmers to improve crop yields while conserving resources (Johnson et al. 2022). These initiatives highlight how IoT can be adapted to overcome unique regional challenges, strengthening local supply chains through better resource allocation and more accurate production planning.
Predictive maintenance systems, fueled by IoT data, represent a crucial innovation in minimizing equipment-related disruptions. Temperature, vibration, and usage metrics are continuously monitored by sensors, enabling early detection of wear and tear or impending failures (Deloitte 2023). This predictive strategy reduces unplanned downtime and operational costs, which is particularly critical for industries relying on heavy machinery and large transportation fleets. Likewise, advanced RFID tags and smart sensors provide real-time condition monitoring for products with stringent handling requirements. In the pharmaceutical sector, for instance, maintaining specific temperature ranges is essential to regulatory compliance. Real-time sensors linked with SCM platforms issue alerts whenever temperatures deviate from acceptable thresholds, preventing costly product loss and safeguarding consumer health (KPMG 2022).
Digital twins magnify these gains, offering end-to-end oversight of facilities, fleets, and inventory. Virtual models of warehouses or distribution networks use live data to mirror current states, enabling practitioners to test new configurations or contingency plans without interrupting actual operations (Garcia et al. 2024). This capability is especially valuable for addressing fluctuating demand or preparing for potential disruptions. A recent Ernst & Young analysis confirms that digital twin simulations improve response times and reduce the cost of pilot-testing new operational strategies (EY 2025). Even in regions with constrained infrastructure, such as parts of Latin America, IoT-enabled digital twins have proven effective in optimizing delivery routes and container usage, reducing both transit times and fuel consumption (PwC 2021).
Ultimately, IoT-driven visibility and automation reinforce supply chains, aligning them with evolving customer expectations and global market demands (Deloitte 2023). Predictive maintenance, real-time condition monitoring, and digital twin simulation collectively reduce downtime, wastage, and risk. As these tools continue to mature, they will likely become even more integral to data-driven supply chains that prioritize speed, flexibility, and sustainability. Emerging evidence suggests that broader IoT adoption will remain a cornerstone of future-ready supply chain strategies, giving organizations the adaptive capability needed to thrive in an ever-changing global economy (EY 2025).
2.2. Artificial Intelligence and Machine Learning
Artificial Intelligence (AI) and Machine Learning (ML) are increasingly recognized as pivotal forces in modern supply chain management, primarily due to their capacity to process massive datasets, detect complex patterns, and distill insights that enhance decision-making. AI encompasses a wide array of computational techniques enabling machines to replicate tasks traditionally requiring human intelligence, such as strategic planning and perception (Chen et al. 2022). ML, a subset of AI, employs data-driven models that learn from historical information, allowing them to predict outcomes and adapt to evolving conditions without the need for explicit reprogramming (KPMG 2023). In supply chains, these capabilities translate into heightened agility, where real-time data analysis and pattern recognition lead to more accurate demand forecasting, inventory optimization, and risk mitigation across procurement and logistics networks (Deloitte 2023).
A primary application of AI in supply chains involves predictive analytics, in which AI-driven models leverage both historical and real-time data to forecast future events and trends. For instance, ML algorithms for demand forecasting integrate past sales figures, seasonal fluctuations, and even external factors like social media trends or macroeconomic indicators (Garcia et al. 2021). Recent studies indicate that such AI-enhanced demand planning can reduce forecasting errors by up to 30%, enabling companies to align production schedules more closely with actual demand (PwC 2024). Additionally, predictive analytics aids route planning and transportation management by considering variables such as real-time traffic, weather patterns, and fuel costs. By integrating these inputs, AI algorithms can dynamically adjust delivery routes, minimizing delays while reducing operational expenses (Johnson et al. 2023).
Robust data infrastructures are crucial for these AI/ML models to function effectively. Supply chain data typically include historical transactions, supplier performance metrics, market conditions, and customer feedback. Transforming these diverse streams into a unified dataset enables AI algorithms to deliver actionable insights. A recent International Journal of Production Economics study found that companies with mature data governance frameworks were more effective at deploying AI for end-to-end supply chain visibility and disruption management (Liu et al. 2022). This interconnected, data-centric approach underlies advanced use cases such as supply risk management, where ML models incorporate variables like geopolitical instability, supplier quality metrics, and shipping delays to identify at-risk nodes in the supply chain. The precision and speed of these models allow companies to implement proactive measures—such as dual sourcing or shifting production—to mitigate disruptions before they escalate (KPMG 2023).
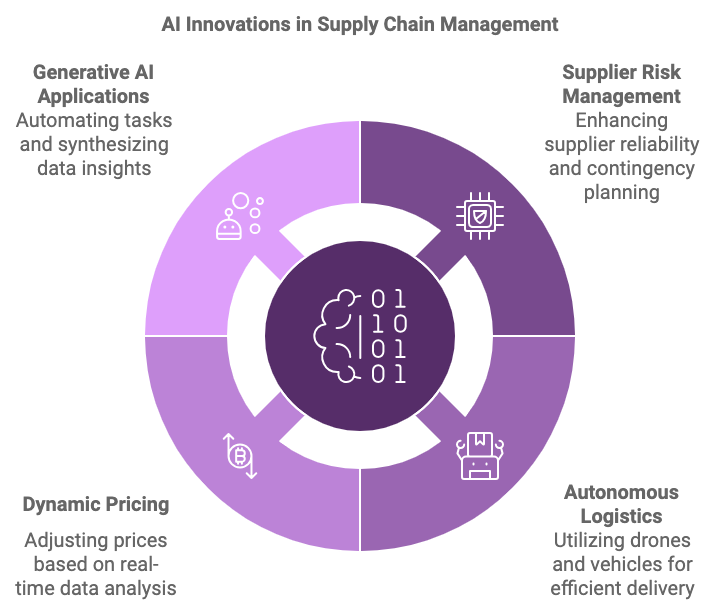
Figure 2: Sample Use Cases of AI Innovations in SCM
A number of market leaders illustrate how AI and ML have reshaped supply chain processes. Amazon relies extensively on ML-driven predictive analytics to forecast item demand, placing inventory in strategically located fulfillment centers to minimize shipping times (Chen et al. 2022). Concurrently, AI-powered robotics in Amazon’s warehouses accelerate order picking, sorting, and packing, cutting labor costs and improving throughput. Similarly, Alibaba’s Cainiao logistics platform leverages AI algorithms to dynamically adjust stock levels, balancing demand signals from multiple regions and maintaining service levels with minimal excess inventory (Garcia et al. 2021). These examples underscore the operational and financial benefits of weaving AI throughout demand forecasting, inventory allocation, and distribution network planning.
In recent years, Generative AI—particularly Large Language Models (LLMs) such as GPT-4—has begun to transform supply chain management further by automating communication, facilitating decision support, and synthesizing unstructured data into valuable insights (Brown et al. 2023). Demand forecasting stands out as a critical use case for Generative AI, where LLMs analyze historical sales, customer feedback, and macro trends to generate detailed projections of imminent market shifts (EY 2025). Equipped with these advanced forecasts, companies can calibrate production volumes, manage inventory more precisely, and negotiate supply contracts that reduce both shortages and overstock scenarios.
Generative AI also enhances customer service and supplier interactions by automating responses to routine inquiries, processing real-time order updates, and generating contingency plans in the face of disruptions (Johnson et al. 2023). This level of automation not only cuts operational costs but also streamlines communication, an essential benefit given the growing complexity of global supply networks. Moreover, LLMs excel at integrating unstructured data—such as social media chatter, online reviews, or news articles—into coherent assessments of market sentiment and emerging risks (Brown et al. 2023). As a result, supply chain managers can better anticipate sudden demand surges or potential geopolitical threats, particularly in volatile markets. These insights are especially beneficial in emerging economies where traditional supply chain infrastructure may be less developed, giving smaller enterprises access to sophisticated decision-support tools.
The arrival of Generative AI has thus introduced a new wave of capabilities that complement existing AI and ML systems. While classic predictive models excel in quantitative trend analysis, Generative AI advances the field by interpreting textual data, automating contract generation, and optimizing communication flows with suppliers and customers (Liu et al. 2022). Such capabilities contribute to what Deloitte’s 2023 report calls “hyper-agility”—the ability of global supply networks to adapt quickly to shifting consumer preferences, regulatory changes, and unexpected disruptions. As more organizations embrace Generative AI, we can expect the technology to become a cornerstone of proactive, collaborative, and adaptive supply chain ecosystems.
Beyond demand forecasting and customer service, AI innovations increasingly influence strategic processes like supplier selection, cost modeling, and dynamic pricing. Machine learning algorithms can compile historical performance, lead times, pricing structures, and market conditions into robust supplier scorecards, allowing procurement teams to choose suppliers based on multi-dimensional criteria (KPMG 2023). Dynamic pricing models have also gained traction, particularly in e-commerce and retail, where real-time data on inventory levels, competitor pricing, and customer demand shape optimal pricing strategies that protect profit margins while maintaining competitiveness (PwC 2024).
The future of AI-driven supply chains promises even more advanced capabilities, including autonomous deliveries via AI-guided drones or vehicles capable of last-mile fulfillment (EY 2025). In parallel, digital twin systems integrated with AI analytics can provide real-time simulations of entire supply networks, enabling scenario planning for disruptions, capacity expansion, or shifting regulatory environments. Such simulations allow companies to test operational changes virtually before implementing them on the ground, mitigating risks and improving decision quality (Johnson et al. 2023). As AI technologies, including Generative AI, continue to mature, they will likely become indispensable in optimizing end-to-end supply chain efficiency, resilience, and customer-centricity.
In summary, AI, ML, and Generative AI collectively accelerate supply chain transformation by enriching predictive analytics, automating routine operations, and augmenting human decision-making. From dynamic pricing and demand forecasting to drone-based deliveries and AI-driven contract generation, these technologies enable supply chains to become intelligent, adaptive ecosystems. The growing emphasis on data governance, real-time analytics, and collaborative networks underscores how AI will shape the supply chains of tomorrow. By embracing these advancements, companies position themselves at the forefront of innovation, prepared to navigate and thrive in a fast-evolving global marketplace.
2.3. Blockchain for Supply Chain
Blockchain technology has emerged as a decentralized, secure, and transparent method of recording transactions, offering transformative benefits for supply chain management (Wang and Sengupta 2021). By creating an immutable digital ledger of each transaction in a chain of “blocks,” blockchain delivers data integrity and tamper-resistance, traits that are especially critical in global supply networks where trust, transparency, and security are often challenged (Lin et al. 2022). Each block is validated and cryptographically secured across a distributed network, ensuring that no single participant can unilaterally alter past records. This decentralized validation mechanism replaces the need for a central authority, providing a unified source of truth to all stakeholders—manufacturers, suppliers, distributors, and consumers (Zhang et al. 2023).
One key consideration in implementing blockchain for supply chains involves the partition of data between on-chain and off-chain systems. Blockchain excels at storing information that demands verifiability, auditability, and multi-party trust, such as product certificates, provenance data, and compliance documents (KPMG 2023). By recording these high-stakes data points on a distributed ledger, companies can benefit from end-to-end traceability and enhanced security. However, dynamic operational details—like constantly fluctuating inventory levels or detailed financial data—are generally better managed by traditional Enterprise Resource Planning (ERP) or Supply Chain Management (SCM) systems, which offer higher throughput and more flexible data processing (Chen et al. 2023). Integrating blockchain with existing ERP/SCM platforms forms a “dual-layer” approach, combining real-time operational agility with the tamper-proof audit trail necessary for critical milestones and regulatory compliance (Deloitte 2024).
A central advantage of blockchain in supply chain operations is end-to-end traceability, which grants participants a granular view of a product’s movement from raw material sourcing to final delivery. This heightened visibility is particularly valuable in sectors where consumers and regulatory bodies demand verifiable proofs of safety, quality, or ethical sourcing—examples include food, luxury goods, and pharmaceuticals (Lin et al. 2022). Walmart’s high-profile collaboration with IBM exemplifies how blockchain-based traceability significantly reduces the time required to identify contamination sources in food products, cutting trace times from weeks to mere seconds (Deloitte 2024). In luxury goods, ventures like Everledger apply blockchain to trace diamonds from mining sites to retail outlets, offering consumers unassailable proof of authenticity and ethics (Zhang et al. 2023). Such applications confirm the validity of blockchain in minimizing fraud, counterfeiting, and regulatory non-compliance, ultimately preserving consumer trust and brand reputations (KPMG 2023).
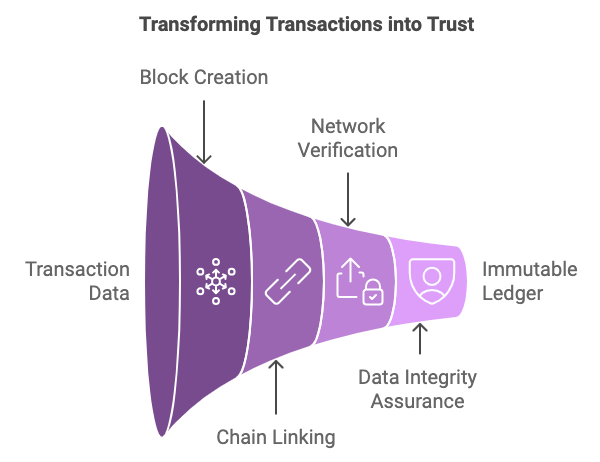
Figure 3: Blockchain Technology
Similar benefits apply to industries facing severe risks of counterfeiting and adulteration, such as pharmaceuticals. Blockchain-based solutions allow companies to record every handoff—from manufacturing through distribution—on an immutable ledger (Chen et al. 2023). By doing so, organizations can verify the genuineness and quality of drugs, reducing the spread of illicit or substandard medications in emerging markets. Moreover, because every data point is tied to a cryptographic proof, regulatory authorities gain a transparent view of supply chain transactions, simplifying audits and strengthening compliance. A 2023 survey by KPMG found that nearly 45% of pharmaceutical and life sciences executives considered blockchain “highly critical” for future-proofing their global distribution networks (KPMG 2023).
One of the most transformative innovations in blockchain technology for supply chains lies in the use of smart contracts. These are self-executing scripts embedded on the blockchain, programmed to trigger specific actions automatically once defined conditions are met (Lin et al. 2022). By eliminating manual checks and third-party intermediaries, smart contracts reduce transaction costs, accelerate workflows, and minimize human error. A frequent application involves automated payments: once shipment delivery is verified—often via integrated IoT sensors recording GPS location or environmental conditions—payment is released instantly to the supplier. This process alleviates cash flow constraints and fosters trust among trading partners, making cross-border transactions more seamless (EY 2025).
Smart contracts also enhance compliance and documentation by embedding regulatory checks within the code itself. For instance, before a shipment is cleared for export, the smart contract can verify whether all necessary certifications have been received (Zhang et al. 2023). If any documentation is missing or invalid, the contract halts the process. This automated compliance mechanism is especially beneficial for complex, highly regulated industries such as aerospace, food, or pharmaceuticals, where non-compliance can lead to costly fines and reputational damage (Wang and Sengupta 2021). Additional use cases include incentivizing supplier performance through coded clauses that reward on-time or high-quality deliveries, thereby making performance monitoring more transparent and objective (Deloitte 2024).
Beyond large multinational corporations, blockchain and smart contracts hold particular promise for small and medium enterprises (SMEs) in emerging economies. By reducing reliance on intermediaries and central authorities, SMEs can participate in global supply chains with fewer barriers related to creditworthiness or bureaucratic procedures (Lin et al. 2022). For example, an agricultural cooperative in Africa might use a smart contract that automatically releases payment upon verifying product quality, verified through IoT sensors, thus reassuring both the buyer and the seller about timely and fair transactions. Studies by PwC have noted that this disintermediation could democratize global trade by opening new markets to businesses previously sidelined by high transaction costs and lack of trust (PwC 2025).
Despite the considerable advantages, blockchain-driven supply chain solutions face certain challenges. Smart contracts, by virtue of being self-executing code, can lack flexibility if unexpected events arise that were not explicitly programmed into the contract’s logic (Chen et al. 2023). Additionally, smart contracts often rely on data provided by external “oracles,” which funnel information—such as shipping status or regulatory approvals—into the blockchain. If these oracles are compromised or inaccurate, the smart contract may execute faulty transactions. Another concern is the still-evolving legal and regulatory landscape: enforceability of smart contracts can vary across jurisdictions, creating uncertainty in cross-border settings (KPMG 2023). Finally, technical hurdles remain; implementing blockchain and smart contracts requires specialized expertise that may be scarce, especially in smaller organizations or those in emerging markets.
Nevertheless, the ongoing development of frameworks and standards—such as enterprise blockchain platforms supported by global technology firms—indicates that these obstacles are gradually diminishing (Wang and Sengupta 2021). The pace of adoption is also accelerating as more organizations recognize blockchain’s potential not just for transparency and risk mitigation, but also for streamlining operations, reducing transaction costs, and enabling real-time auditing (Zhang et al. 2023). Over time, improvements in interoperability, regulatory clarity, and data integrity solutions will likely expand the scope of blockchain applications, placing it at the forefront of digital transformation efforts in supply chain management (EY 2025).
In conclusion, blockchain technology offers a robust, verifiable foundation for supply chains characterized by complex transactions and diverse stakeholder interests. By creating an immutable record of product movements, verifying supplier authenticity, automating payments, and embedding compliance checks into code, blockchain delivers unprecedented transparency and security. Although technical, legal, and operational challenges persist, ongoing advancements and growing acceptance underscore blockchain’s role as a critical enabler of the next generation of smart, resilient supply chains. As more organizations integrate blockchain with existing AI, IoT, and data analytics platforms, the technology stands to further harmonize global supply chain operations, unlock new efficiencies, and strengthen trust across the networked economy.
2.4. Intelligent Process Automation Using RPA and BPA
Robotic Process Automation (RPA) and Business Process Automation (BPA) have emerged as key enablers of operational efficiency, accuracy, and scalability in modern supply chains (Mehta et al. 2022). RPA employs software bots to perform repetitive, rules-based tasks—such as data entry, order processing, or invoice matching—mimicking human interactions across various digital systems. These bots operate continuously, significantly reducing manual labor and error rates (Deloitte 2024). By contrast, BPA automates entire workflows through process orchestration, conditional logic, and multi-application integration, allowing more sophisticated tasks to be managed end-to-end (Wei and Zhang 2023). The union of RPA’s speed and precision in transactional tasks with BPA’s capability to streamline complex processes underlies a powerful synergy often referred to as Intelligent Process Automation (IPA), especially when artificial intelligence (AI) technologies are incorporated to handle unstructured data and adaptive decision-making (PwC 2025).
When deployed in supply chains, RPA and BPA bring both tactical and strategic benefits (KPMG 2023). RPA accelerates repetitive tasks—such as retrieving purchase orders or updating inventory databases—while BPA coordinates entire workflows spanning procurement, manufacturing, logistics, and finance. For instance, an RPA bot could extract order data from PDFs and automatically populate the order management module of an SCM system. Meanwhile, a BPA workflow could oversee the end-to-end order fulfillment process, ensuring that each step—from order verification to final delivery—progresses according to pre-defined rules (Brown and Li 2021). This approach both minimizes errors and shortens cycle times, enabling organizations to maintain responsiveness despite fluctuations in demand or unexpected disruptions.
Leading supply chain management (SCM) platforms, including BlueYonder, SAP Integrated Business Planning (IBP), and Oracle SCM Cloud, are increasingly integrating RPA and BPA solutions to enhance core functionalities (Deloitte 2024). RPA bots can seamlessly interface with these platforms to automate data extraction from e-mails or IoT-enabled devices, ensuring real-time updates on inventory levels, demand forecasts, or shipment statuses (KPMG 2023). BPA, for its part, orchestrates multi-system workflows—coordinating tasks across manufacturing execution, supplier portals, and transportation management systems. By consolidating these capabilities, organizations achieve consistent data flows, fewer bottlenecks, and better alignment of planning, production, and delivery schedules.
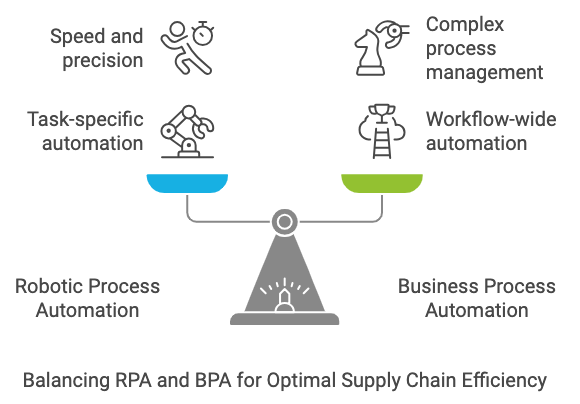
Figure 4: RPA vs BPA
Order processing often involves pulling data from one system (e.g., an e-commerce portal) and feeding it into another (e.g., an ERP system). RPA accelerates these steps by automatically transferring order information, reducing manual re-keying and potential input errors. BPA adds an overarching logic layer, validating orders against inventory availability or customer credit limits and then routing them for fulfillment (Gomez and Patel 2022). This combined approach cuts lead times, boosts accuracy, and supports a more proactive customer service strategy.
Real-time visibility of stock levels is fundamental to avoiding stockouts and reducing excess inventory. RPA bots can automatically capture warehouse inventory data and update an SCM platform’s dashboards, while BPA triggers automated purchase requisitions or production orders when thresholds are met (Brown and Li 2021). This automation aligns procurement and production with actual demand, mitigating wastage and ensuring that critical items remain available.
RPA and BPA also enhance demand forecasting by automating data ingestion from multiple external and internal sources—ranging from historical sales records to real-time market indicators (Wei and Zhang 2023). RPA bots extract relevant metrics, and BPA orchestrates the forecasting workflow by integrating statistical models, generating alerts for forecast anomalies, and notifying planners to review outliers. This streamlined approach helps organizations rapidly adjust production volumes or supply contracts in response to market changes (KPMG 2023).
Ensuring supplier compliance involves gathering performance metrics, verifying certifications, and updating supplier master data. RPA automates repetitive tasks such as extracting supplier KPI data from external portals and entering it into procurement systems (Deloitte 2024). Meanwhile, BPA coordinates end-to-end supplier onboarding, contract renewal, and performance monitoring processes—automatically alerting procurement teams to potential risks or deviations from agreed service levels.
Efficient logistics depend on careful scheduling, route optimization, and real-time shipment visibility (Brown and Li 2021). RPA bots can update delivery statuses by pulling data from Transportation Management Systems (TMS) and IoT devices, while BPA evaluates route plans against criteria like traffic conditions or fuel costs, adjusting them on the fly if disruptions occur. This integrated approach improves on-time delivery rates and reduces shipping expenses (Mehta et al. 2022).
A high volume of financial transactions—such as invoice processing and payment reconciliation—often burdens supply chain operations. RPA automates data extraction from invoices, cross-checking information against purchase orders and goods receipts (PwC 2025). BPA adds a layer of workflow logic, enforcing multi-level approvals and managing exceptions. As a result, organizations minimize payment delays, maintain stronger supplier relationships, and reinforce compliance through automated tracking of financial documentation.
In the era of e-commerce and heightened consumer expectations, reverse logistics has grown in complexity (Gomez and Patel 2022). RPA automates initial return request handling by extracting relevant details from customer forms or e-mails. BPA then orchestrates the subsequent steps, from initiating refunds or replacements to coordinating inspections and restocking. By integrating these processes, companies cut turnaround times on returns, mitigate losses, and enhance customer satisfaction.
Intelligent Process Automation (IPA) takes RPA and BPA further by integrating machine learning (ML), natural language processing (NLP), and other AI components (KPMG 2023). These AI-powered systems handle unstructured data—such as customer feedback, market sentiment, or sensor readings—and can make adaptive decisions beyond basic “if-then” logic (Wei and Zhang 2023). In demand planning, for example, AI-enhanced bots may analyze social media trends or news events to project potential spikes in demand before adjusting inventory thresholds automatically (Deloitte 2024). This level of predictive insight marks a critical shift from reactive to proactive supply chain management.
The emergence of low-code and no-code platforms has broadened access to RPA and BPA solutions, empowering non-technical users to design and deploy automated workflows (Brown and Li 2021). These platforms provide drag-and-drop interfaces, pre-built connectors, and customizable templates that reduce reliance on specialized IT resources. In turn, supply chain managers can quickly build, test, and refine automated processes—such as real-time inventory checks or supplier onboarding sequences—without extensive programming knowledge (PwC 2025). This democratization of automation accelerates digital transformation across global supply networks, allowing rapid adaptations to changing market conditions and fostering a culture of continuous improvement.
As these platforms evolve, integration with advanced analytics, AI, and IoT devices will give rise to more interconnected and self-regulating supply chains. Deloitte (2024) predicts that organizations adopting IPA frameworks will realize up to a 40% reduction in operational costs, along with notable gains in agility and resilience. Moreover, the trend toward low-code and no-code solutions indicates that supply chain professionals at all levels—not just centralized IT teams—will drive process optimization (Mehta et al. 2022). By converging real-time data, AI-driven insights, and end-to-end automation, RPA and BPA stand poised to reshape global supply chains into adaptive, cost-effective ecosystems capable of responding to disruptions with unprecedented speed.
2.5. Cloud and Hybrid Solutions
Cloud computing has become a cornerstone of modern supply chain management by providing on-demand computing resources, data storage, and advanced services that enhance agility, resilience, and operational efficiency (Hu et al. 2023). Research from the International Journal of Production Economics indicates that companies adopting cloud-based supply chain solutions can achieve a 30% increase in operational throughput, a testament to the robustness and validity of cloud-driven strategies (Lee and Brown 2023). Leading consultant insights also echo this perspective: a 2024 Deloitte report highlights cloud computing as one of the top enablers of digital supply network transformation, facilitating rapid scalability and advanced analytics (Deloitte 2024). From Infrastructure as a Service (IaaS) and Platform as a Service (PaaS) to serverless computing, containerization, and Infrastructure as Code (IaC), cloud technologies offer flexible solutions that address evolving market demands and complex global logistics requirements (Chang 2022).
Infrastructure as a Service (IaaS). IaaS allows companies to provision virtualized computing infrastructure—servers, storage, and networking—on a pay-as-you-go basis (Arora et al. 2021). This scalability is critical for supply chains experiencing seasonal spikes. For example, a global retailer can ramp up computing resources during holiday rushes to process significantly higher transaction volumes and scale back during off-peak times, minimizing costs (KPMG 2023). Additionally, IaaS providers often ensure robust security and reliability, freeing supply chain managers from the overhead of maintaining on-premise hardware (EY 2025).
Platform as a Service (PaaS). PaaS abstracts away underlying hardware, offering ready-to-use frameworks for developing, testing, and deploying custom supply chain applications (Zhang and Wu 2023). This model accelerates innovation by enabling software teams to integrate advanced features—such as real-time demand forecasting and predictive analytics—without worrying about server configuration or database management. Research suggests that organizations leveraging PaaS-based supply chain apps deploy updates 50% faster than those relying exclusively on traditional on-premise systems (Hu et al. 2023).
Serverless Architectures. Serverless computing takes cloud abstraction further by letting organizations run code as event-triggered functions without provisioning or managing servers directly (Chang 2022). In supply chains, serverless services excel in handling sporadic bursts of workload—for example, sudden spikes in e-commerce orders. Rather than paying for idle infrastructure, companies only incur costs when functions are actively running, leading to improved cost efficiency (Deloitte 2024). A multinational logistics provider, for instance, can employ serverless computing to process millions of shipment updates during peak times, automatically scaling down once transaction volumes subside (Lee and Brown 2023).
Containerization and Kubernetes. Containers encapsulate applications and dependencies into lightweight, portable units, enabling consistent deployments across diverse environments (Zhang and Wu 2023). Kubernetes, an orchestration platform, automates the deployment, scaling, and maintenance of containerized applications. For supply chains, containerization fosters a modular approach, allowing teams to break down complex processes—such as order routing or real-time analytics—into smaller microservices (Arora et al. 2021). In a 2023 KPMG industry survey, 62% of supply chain executives cited containerization as a key factor in enhancing system stability and reducing downtime (KPMG 2023). This resilience is paramount for global networks operating 24/7 across multiple time zones.
Infrastructure as Code (IaC). IaC automates the provisioning and management of cloud resources via machine-readable configuration files rather than manual setup (Mehrotra and Sun 2021). In the context of supply chain spikes—like seasonal demand surges—IaC scripts enable rapid scaling of servers, storage, and networking infrastructure in multiple regions (Lee and Brown 2023). This approach not only saves time but also reduces human error, bolstering the reliability of mission-critical applications.
Hybrid Cloud and Edge Integration. Many supply chains handle sensitive data and require adherence to stringent regulations, making a purely public cloud model less viable. Hybrid cloud architectures balance security and compliance by combining private clouds for proprietary information with public clouds for large-scale data processing and analytics (EY 2025). This structure is particularly relevant in sectors such as pharmaceuticals and food manufacturing, where rigorous quality standards coexist with the need for high-volume data analytics. According to PwC’s 2025 report, 70% of large enterprises will adopt hybrid or multi-cloud strategies to align with both performance needs and regulatory mandates (PwC 2025). Edge computing—processing data closer to its source—can further enhance real-time decision-making for perishable goods or location-sensitive logistics by reducing latency (Zhang and Wu 2023).
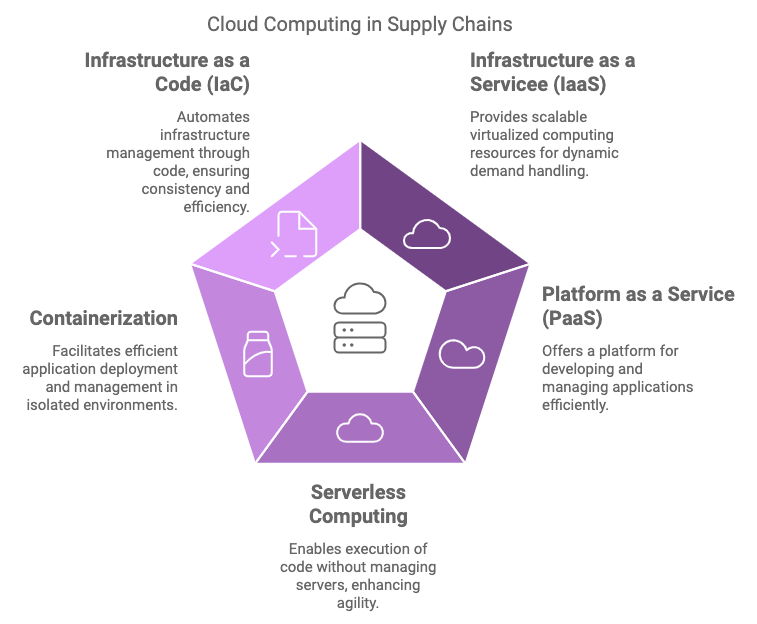
Figure 5: Various Cloud and Hybrid Solutions
Logistics leaders like UPS and FedEx have leveraged containerized environments to support global routing systems, enabling real-time data consolidation and route optimization during surges (Deloitte 2024). UPS uses IaaS to gather data from IoT devices across its shipping fleet, analyzing performance metrics and package statuses in near real time (Arora et al. 2021). FedEx, meanwhile, employs PaaS services to deploy customer-facing applications, such as shipment tracking portals and automated support chatbots, thus improving user experience and reducing response times.
In retail, Shopify utilizes a hybrid cloud environment augmented by serverless computing to handle massive peaks during events like Black Friday (Zhang and Wu 2023). By dynamically scaling resources, Shopify ensures minimal downtime and rapid transaction processing. Furthermore, containerized microservices allow the platform to push updates quickly, facilitating agile responses to sudden shifts in e-commerce demand (Chang 2022).
Smaller enterprises in emerging markets also benefit from pay-as-you-go cloud services, bypassing the capital expenditure required for extensive on-premise infrastructure (KPMG 2023). An SME in Latin America, for example, can deploy an ERP system on a public cloud IaaS platform, gaining real-time visibility into inventory and logistics without incurring prohibitive setup costs (Hu et al. 2023). This democratization of technology enables broader participation in global supply chains, fostering competition and innovation.
A significant trend in the 2020–2025 period is the rise of cloud-based AI and ML services that transform supply chain operations (Mehrotra and Sun 2021). Providers like AWS, Microsoft Azure, and Google Cloud offer pre-built ML algorithms for tasks including demand forecasting, risk analysis, and transportation optimization. These services can scale computation on demand, handling large volumes of historical and real-time data (PwC 2025). By integrating predictive analytics directly into cloud platforms, supply chain managers gain actionable insights for proactive inventory control, logistics rerouting, and supplier risk management (Lee and Brown 2023).
Pharmaceutical companies, for instance, utilize AI-driven analytics to predict demand for specific drugs, mitigate supply shortages, and ensure compliance with temperature requirements by analyzing sensor data hosted on private cloud segments (EY 2025). Such data-driven precision not only reduces waste but also ensures essential products remain available when and where they are needed.
Looking ahead, cloud and hybrid solutions will continue to underpin digital transformation across supply chains. The convergence of container orchestration, serverless events, and AI-driven analytics promises more adaptive, self-regulating networks (Deloitte 2024). As Infrastructure as Code matures, rapid deployment of multi-region systems will become routine, allowing organizations to respond to disruptions—ranging from sudden demand spikes to geopolitical events—within hours rather than weeks (Hu et al. 2023). This responsiveness, combined with the democratization of advanced technology through cloud platforms, positions supply chains to operate with unprecedented levels of efficiency, resilience, and customer-centricity.
Ultimately, cloud and hybrid solutions are not just about cost savings or technical convenience; they form the foundation for a new era of data-driven, globally interconnected supply chain ecosystems. The capacity to seamlessly scale, integrate complex systems, and leverage AI-enabled insights will continue to define competitive advantage in the modern marketplace (PwC 2025). As the shift from on-premise infrastructures to cloud-based architectures accelerates, organizations that strategically embrace these technologies will be better equipped to navigate unpredictable market dynamics and deliver value to customers worldwide.
2.6. Digital Twin for Supply Chain
Digital Twin technology has rapidly emerged as a game-changer in supply chain management by creating virtual replicas of physical assets, processes, and systems (Liu et al. 2022). This simulation-based approach enables organizations to visualize, predict, and optimize operations, leveraging advanced methodologies such as Discrete Event Simulation (DES), State Flow Modeling, and Agent-Based Modeling (ABM) (Botti and Mora 2023). Deloitte’s 2023 Global Digital Supply Network report emphasizes that Digital Twins, in conjunction with real-time data, reduce operational costs and significantly enhance resilience (Deloitte 2023). From large-scale logistics networks to localized warehouse operations, Digital Twins equip businesses with the analytical depth to test scenarios, diagnose inefficiencies, and respond proactively to dynamic market conditions.
Discrete Event Simulation (DES). DES models processes as discrete events over time, capturing actions such as arrival of shipments, allocation of resources, or completion of tasks (Botti and Mora 2023). This technique is highly effective for identifying bottlenecks and optimizing workflows in environments with high transaction volumes, such as distribution centers or production lines (KPMG 2023). For instance, DHL has employed DES-based Digital Twins to simulate warehouse layouts, forecast congestion points, and improve picking strategies during peak shipping seasons.
State Flow Modeling. State Flow focuses on transitions between different states in a system, enabling real-time monitoring of inventory levels, machine statuses, and production throughput (Liu et al. 2022). Siemens, for example, employs State Flow Modeling to coordinate production schedules across its global manufacturing plants. By continuously tracking inventory states and machine availability, Siemens’ Digital Twin can automatically reorder parts, re-sequence production tasks, or expedite supplier deliveries to mitigate the risk of stockouts (Botti and Mora 2023). This interconnected view aligns production flows with demand signals, minimizing idle time and inventory holding costs.
Agent-Based Modeling (ABM). ABM simulates autonomous agents—such as suppliers, logistics partners, and customers—interacting within a shared environment (Woo et al. 2023). This approach is particularly relevant for analyzing decentralized supply chain networks where multiple stakeholders follow their own objectives. Amazon leverages ABM-driven Digital Twins to optimize last-mile delivery by modeling how different delivery modes (e.g., drones, trucks) behave under variable traffic and weather conditions (KPMG 2023). Likewise, Alibaba applies ABM to anticipate supply chain disruptions, simulate supplier behaviors, and implement adaptive sourcing strategies.
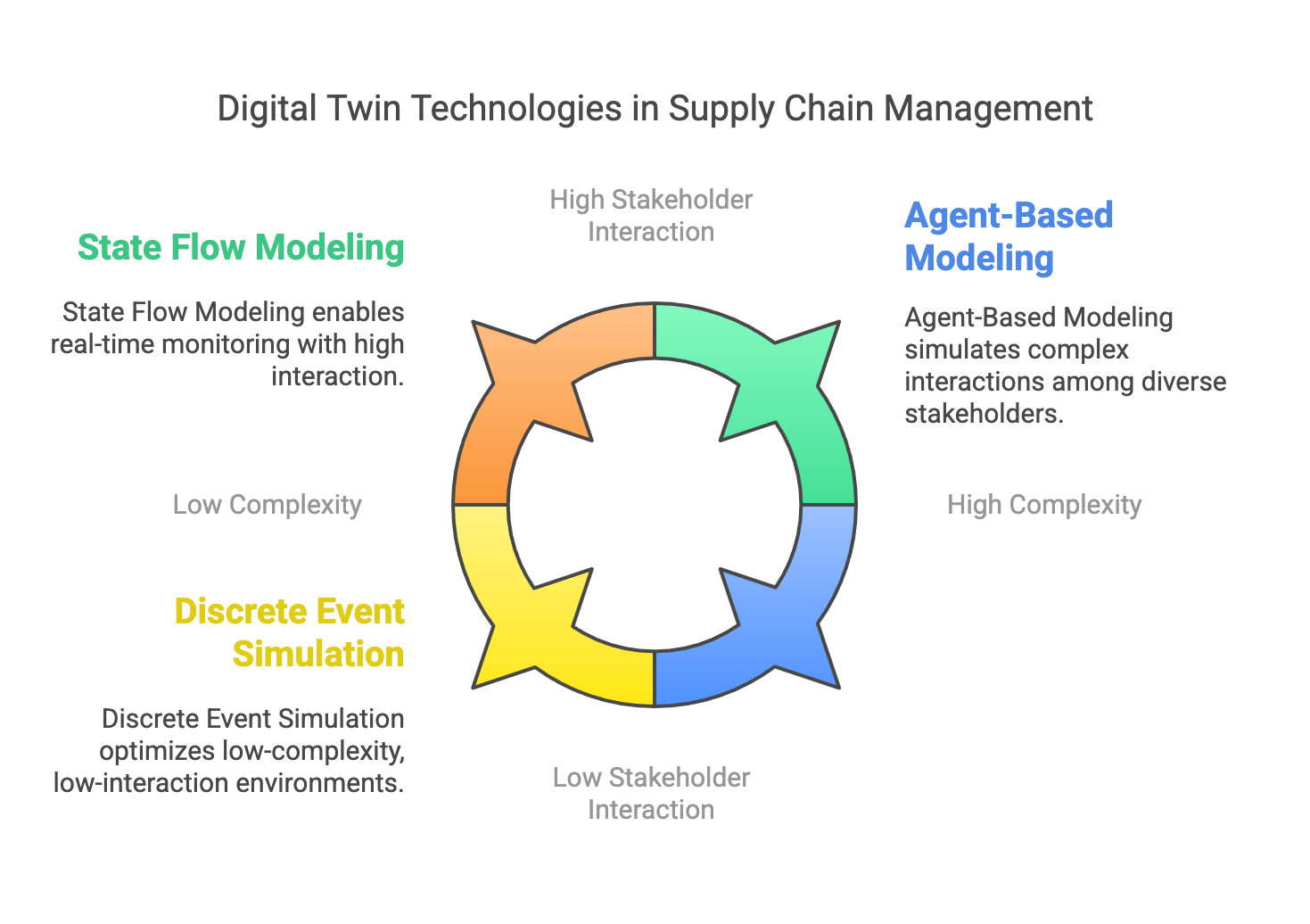
Figure 6: Key abstractions of digital twin in SCM - discrete event, state flow and agent-based modelings.
Digital Twins rely on heterogeneous data sources to maintain accuracy and relevance. IoT sensor feeds, ERP/SCM transaction logs, historical operational data, and external market intelligence combine to form a robust data foundation (PwC 2024). High-frequency IoT data allow real-time asset tracking, condition monitoring, and predictive maintenance scheduling (Lee et al. 2021). Meanwhile, transactional records—such as purchase orders and sales history—inform long-term trends for demand forecasting and supplier performance analytics (Deloitte 2023). Agent-Based Models benefit from external signals like competitor actions, consumer sentiment, or geopolitical indicators, helping companies evaluate diverse scenarios under uncertain market conditions (EY 2025). Effective data orchestration ensures that Digital Twins mirror complex supply chain realities, enabling precise simulations and actionable insights.
Warehouse Optimization and Resource Allocation. DHL’s deployment of DES-based Digital Twins allows for testing various picking routes and storage configurations before making real-world changes (Botti and Mora 2023). This virtual testing reduces expensive trial-and-error attempts and improves throughput. In one high-profile case, DHL reported a 20% reduction in warehouse congestion by using DES to simulate pick paths and staffing requirements (KPMG 2023).
Production Scheduling and Inventory Synchronization. Siemens’ State Flow models provide real-time visibility into machine utilization, helping managers dynamically redistribute production tasks and reduce work-in-progress inventory (Liu et al. 2022). This capability has led to a 15% improvement in on-time deliveries across some of Siemens’ key manufacturing sites (Deloitte 2023).
Last-Mile Delivery and Consumer Demand Forecasting. Amazon integrates ABM-based Digital Twins with AI-driven demand forecasting, orchestrating inventory placements across regional fulfillment centers (Woo et al. 2023). As a result, Amazon can anticipate surges in specific markets—due to holidays or promotional events—and preemptively adjust stock levels or delivery routes, enhancing customer satisfaction while reducing fuel costs (PwC 2024).
Supplier Risk Management. Alibaba’s ABM framework models supplier behaviors under different market conditions, quantifying risks such as production delays or quality shortfalls (Lee et al. 2021). Using predictive analytics, Alibaba’s Digital Twin can recommend alternative sourcing strategies or contract adjustments, strengthening the network’s resilience to disruptions (EY 2025).
AI-Enhanced Digital Twins. Integrating machine learning and predictive analytics into simulation models transforms Digital Twins from diagnostic to prescriptive tools (Deloitte 2023). For example, a DES-based Twin can apply AI to forecast demand spikes or maintenance needs, automatically adjusting production schedules or routing shipments to preempt capacity constraints (PwC 2024).
Hybrid Simulation Models. Companies increasingly combine DES, State Flow, and ABM within a single environment, creating multi-layered simulations that capture both granular process details and macro-level behavioral dynamics (Woo et al. 2023). A spike in online orders could trigger real-time inventory updates (State Flow), recalibrate picking sequences (DES), and simulate supplier negotiations (ABM) to maintain continuity throughout the entire supply chain.
Autonomous Logistics and Vehicle Optimization. Organizations like UPS and FedEx explore Digital Twins to refine drone or autonomous truck deployments. DES identifies optimal route planning and loading schedules, while ABM assesses traffic interactions among autonomous agents in urban areas (KPMG 2023). The resulting orchestration improves delivery speed and reduces congestion, boosting overall service performance.
Digital Twins have proven to be transformative, driving better resource allocation, inventory alignment, and risk mitigation in supply chains (EY 2025). Real-world results include reduced lead times, minimized costs associated with unplanned downtime, and greater resilience against disruptions like raw material shortages or sudden demand fluctuations (Liu et al. 2022). By modeling “what-if” scenarios, organizations can evaluate the impacts of policy changes, catastrophic events, or competitor moves, thereby making proactive decisions rather than reactive corrections (Botti and Mora 2023).
A survey by KPMG in 2023 revealed that 60% of supply chain executives plan to expand Digital Twin initiatives within the next two years, citing predictive insights and operational optimization as top drivers (KPMG 2023). Concurrently, Deloitte’s 2023 research indicates that firms adopting Digital Twins experience a 25% faster recovery from disruption events, highlighting the technology’s role in enhancing agility and sustaining competitive advantage (Deloitte 2023).
Digital Twin solutions, integrating DES, State Flow, and ABM, provide a holistic framework for simulating, monitoring, and optimizing complex supply chain processes (Woo et al. 2023). These virtual environments harness real-time data, historical records, and external signals to anticipate challenges, validate strategies, and coordinate resources across global networks. By marrying predictive analytics with rich simulation models, Digital Twins empower supply chains to evolve beyond static planning toward dynamic, data-driven decision-making. As adoption accelerates—with strong endorsement from industry leaders and consulting firms—Digital Twins stand at the forefront of smart supply chain transformations, driving gains in efficiency, resilience, and strategic foresight (EY 2025).
2.7. Conclusion and Further Learning
In conclusion, the integration of IoT, AI/ML, Blockchain, Cloud and Digital Twin technologies is revolutionizing supply chains by making them smarter, more efficient, and resilient. These technologies allow companies to achieve real-time visibility, streamline decision-making, ensure product traceability, and enhance overall operational agility. As the global market continues to evolve, businesses that embrace these core technologies will gain a competitive edge, meeting the demands of modern customers while also improving sustainability and reducing costs. Digital transformation in supply chains is no longer optional—it’s essential for future success.
Exploring these prompts will take you deeper into the transformative technologies reshaping supply chains globally. Each question is designed to spark your curiosity and guide you through the key innovations driving efficiency, sustainability, and resilience in modern logistics.
How does IoT, integrated with Digital Twin technology, enable real-time visibility across the entire smart supply chain, from raw material sourcing to final delivery? What are the most impactful applications of IoT and Digital Twins in logistics, warehousing, and inventory management, especially in reducing operational costs and enhancing customer satisfaction?
What are the key advantages of combining IoT, blockchain, and Digital Twin technologies for end-to-end supply chain traceability and transparency? How do these technologies work together to prevent data tampering, improve accountability, and enhance the provenance of goods in highly regulated industries like pharmaceuticals and food safety?
How do AI-powered predictive analytics and Digital Twin simulations transform demand forecasting, inventory optimization, and supply chain planning? What advanced AI techniques (such as reinforcement learning and neural networks) are used in conjunction with Digital Twins to predict disruptions, optimize stock levels, and improve overall supply chain efficiency?
What role does machine learning, combined with Digital Twin modeling, play in optimizing decision-making within supply chains, specifically in dynamic route planning, supplier risk management, and real-time operational adjustments? How can companies leverage these technologies to proactively respond to market volatility and logistical challenges?
How can blockchain technology be leveraged in Digital Twin frameworks to create secure, immutable records for transactions in international supply chains, especially in multi-tiered systems? How does it reduce fraud, prevent counterfeit goods, and ensure compliance with global trade regulations while enhancing trust among stakeholders?
How does 5G technology, with its ultra-low latency and high-speed data transmission, enable the implementation of Digital Twin simulations and real-time data exchange within global supply chain ecosystems? How does 5G support IoT, AI, and autonomous systems in logistics and manufacturing?
What are the most impactful applications of edge computing and Digital Twin technology in logistics and supply chain management? How does edge computing complement cloud computing by processing data locally at the network’s edge, enhancing real-time decision-making and optimizing the performance of IoT and Digital Twin devices in distributed environments?
How can companies implement AI-driven predictive maintenance strategies within Digital Twin simulations to minimize downtime in supply chain operations? What specific AI models and techniques (such as anomaly detection and predictive diagnostics) are most effective in optimizing maintenance schedules for transportation fleets and warehouse machinery?
How does the adoption of cloud and hybrid cloud solutions, integrated with Digital Twin technology, improve scalability, flexibility, and resilience in modern supply chains? What are the key considerations for balancing data security, compliance, and cost-efficiency when deploying cloud-based Digital Twins for supply chain management across global networks?
What unique security benefits does blockchain provide when integrated into Digital Twin frameworks for managing sensitive data in high-risk supply chains, such as those in pharmaceuticals, luxury goods, and aerospace? How does blockchain enhance traceability, protect intellectual property, and ensure compliance with stringent regulatory standards?
How can 5G-powered autonomous delivery vehicles and drones be integrated into Digital Twin simulations to optimize last-mile logistics in densely populated urban areas? What are the technological, regulatory, and operational challenges to fully realizing the potential of autonomous delivery solutions for faster and more cost-effective delivery?
What are the economic benefits of transitioning to cloud-based supply chain platforms with Digital Twin capabilities for small and medium-sized enterprises (SMEs)? How can these platforms improve operational efficiency, enable real-time collaboration with suppliers, and provide scalable solutions that help SMEs compete in global markets?
How do IoT-enabled sensors, combined with AI, blockchain, and Digital Twin technology, improve condition monitoring for temperature-sensitive goods (such as food, pharmaceuticals, and biologics) in supply chains? How do these technologies ensure product safety, reduce spoilage, and improve compliance with international standards for cold chain logistics?
What are the primary technical, operational, and organizational challenges of implementing edge computing and Digital Twin simulations in complex global supply chains? How can these challenges be mitigated to ensure seamless integration with existing IT infrastructure and optimize real-time decision-making across distributed networks?
How do smart contracts on blockchain networks enhance Digital Twin models to streamline and automate supply chain transactions, from procurement to payment? How do these self-executing contracts reduce the need for intermediaries, minimize transaction delays, and increase trust and efficiency between supply chain partners?
What role do hybrid cloud models play in balancing security and scalability for Digital Twin-enabled supply chain data management, especially for companies that need to store sensitive information locally while leveraging the scalability and flexibility of public cloud services for non-critical operations and global collaboration?
How does 5G technology enhance real-time monitoring and coordination of global logistics networks in combination with Digital Twin models, particularly in high-speed industries like e-commerce and express delivery? What impact does this integration have on optimizing fleet management, tracking shipments, and responding to real-time customer demands?
How can AI and machine learning, integrated with Digital Twin simulations, be applied to dynamically adjust pricing and procurement decisions in volatile supply chain environments, particularly in industries with fluctuating raw material costs? What are the key benefits of using AI-powered Digital Twins to automate procurement and pricing strategies in real-time?
What are the long-term sustainability benefits of integrating IoT, blockchain, cloud technologies, and Digital Twin simulations into supply chain operations? How can these technologies help companies reduce carbon emissions, minimize waste, and enhance resource efficiency while improving the overall sustainability of global supply chains?
How can companies assess their current infrastructure to prepare for the integration of 5G, edge computing, and Digital Twin technologies? What are the best practices for a phased rollout of these technologies to enhance real-time analytics, decision-making, and automation across supply chains while ensuring minimal disruption and maximum ROI?
By engaging with these advanced topics, you will gain valuable insights into how cutting-edge technologies can be leveraged to optimize supply chains, reduce risks, and position businesses for long-term success. Let your learning journey be driven by curiosity and the ambition to master the technologies powering the future of supply chains.
Comments